The current collaboration with Eurocircuits has greatly contributed to the project, as it has helped the Da Vinci Satellite team go further into the testing phase. The team is now in a delicate phase: right at the finishing design touches, and about to begin more intensive and integrated testing campaigns. This means that we have to finalize our designs, order material, and simultaneously develop protocols and procedures to ensure the safety of our software, hardware and team members during testing.
At this key moment in the project, is where Eurocircuits’ role came into play. Our project consists of a 2U cubesat, so a small satellite which is the size of a milk carton more or less. In the satellite, all of our subsystems are stacked on top of one another, and the functioning of the satellite heavily depends on their interconnection. To ensure that everything functions as expected, both on Earth and in Space, we must be certain that all subsystems can function on their own standing and in relation to the other subsystems.
Our current testing protocol involves the development of some testing boards, which we refer to as EGSE: electronic ground support equipment. These testing boards will first function as equipment to finetune the driver for each subsystem. In this scenario, the code for the driver will be tested multiple times on the hardware, and a testing board ensures that no damage is done to the latter. After the driver development is complete, we plan to use the testing boards for integrated testing, so by connecting multiple subsystems.
Our current project in collaboration with Eurocircuits focuses on two testing boards for our driver development and further integrated testing: the antenna testing board and the EPS (electrical power system) testing board.
The Antenna EGSE includes the connector to the antenna, two banana plug jacks, for ground and voltage in connections respectively, and, lastly, a MSP-EXP432P401R, the launchpad development kit. The board is designed such that the MSP can be stacked on top of it, and also removed when not required. An input voltage of 3.3V is needed for the board’s functionalities. The EGSE attaches to the antenna via a 9-pin D-subminiature connector, facilitating the communication between the antenna and the MSP.
The electrical power system (EPS) EGSE is equipped with the PC104 and umbilical connection the EPS would normally have connected when assembled in the satellite. This way the EPS can be powered and turned like it is in operational mode. The board also includes two 15-pin headers for plugging in an Arduino Nano BLE33 Sense to enable I2C communications between a PC and the EPS. This way commands can be sent to the subsystem or data can be retrieved. Furthermore, the EGSE is equipped with testing points that can be used to read out values from the output bus as well as to hook up an oscilloscope to the I2C lines. The apply-before-flight and kill switches can be controlled by physical switches on the EGSE itself. The EGSE has a 5 V power input via micro USB to power the board itself and a separate 8.4 V power input to power the EPS through the EGSE.
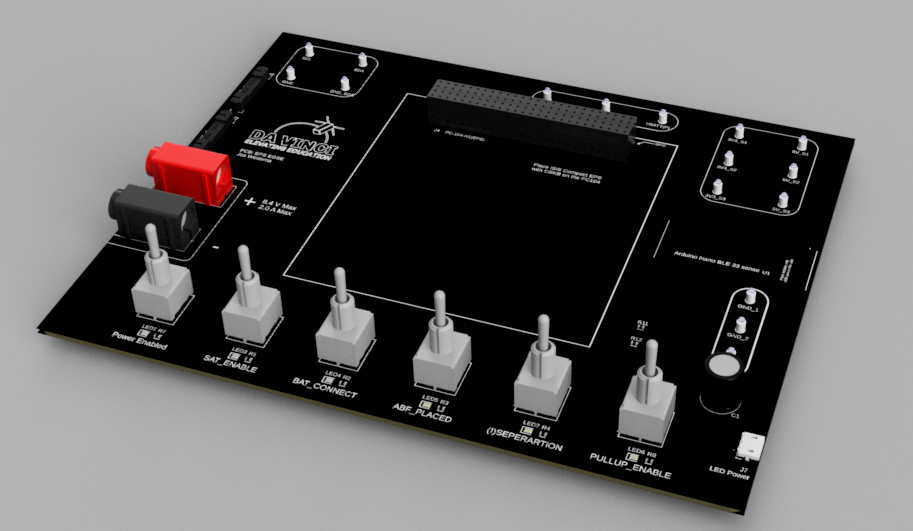
Render of the EPS EGSE populated board. On the bottom, one can see the test switches, while on the top, the PC104 connector that allows us to place the satellite EPS module is visible.
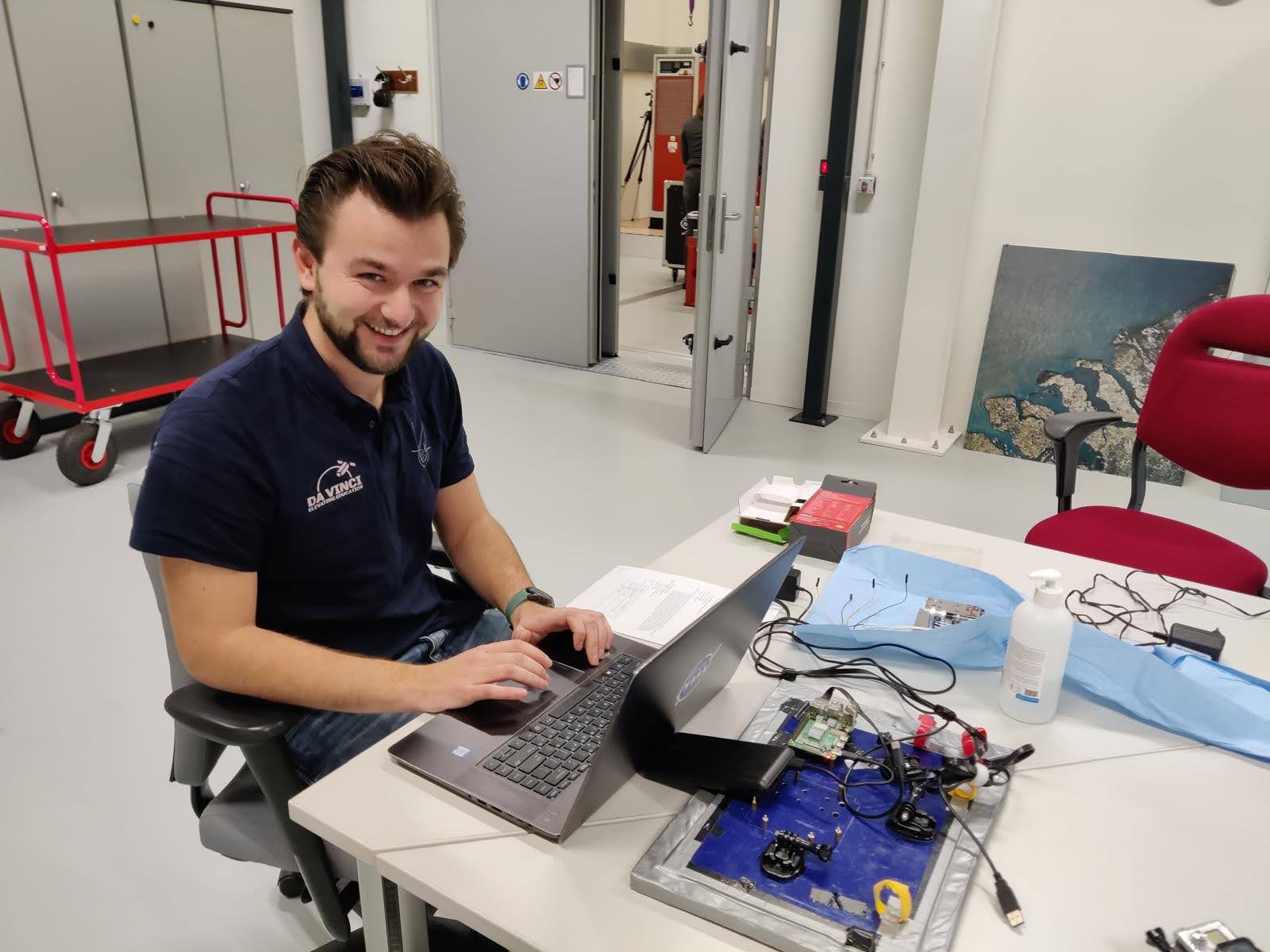